Inventory holding costs are a burden for many businesses, often eating into profit margins. Did you know these costs can account for up to 25% of the total inventory cost? This blog post offers practical solutions to reduce your inventory holding expenses and optimize your bottom line.
Let’s dive in and explore how better management strategies can cut down on these unnecessary expenditures.
Key Takeaways
- Establishing the correct reorder point is crucial in reducing inventory holding costs.
- Optimizing minimum order quantities can help minimize inventory holding costs and improve profitability.
- Avoid overstocking to minimize stock-carrying expenses and reduce inventory management expenses.
- Getting rid of deadstock helps free up valuable storage space and avoid expenses associated with unsellable items.
How to Reduce Inventory Holding Costs
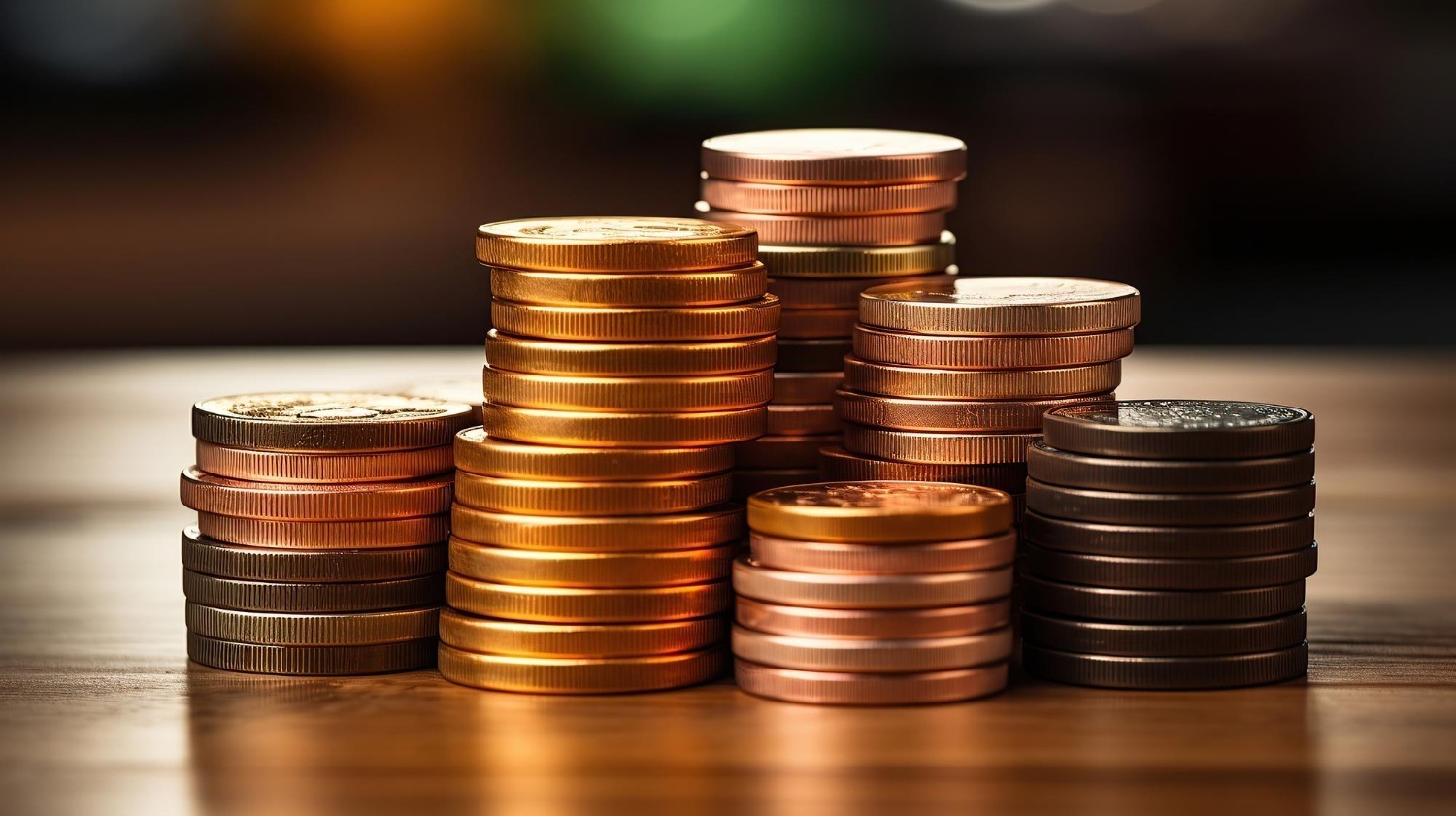
– Get the right reorder point to prevent overstocking or running out of stock.
Get the right reorder point
Establishing the correct reorder point is crucial in reducing inventory holding costs. This refers to the quantity level at which a new order must be placed to re-stock an item in your inventory.
Having these set points accurately calculated helps avoid overstock and understock situations. You can determine these points by considering factors such as average daily sales volume, lead time, maximum and minimum stock levels.
Efficiently managing reorder points ensures continuous production or sales processes, minimizing costly disruptions due to stockouts while preventing surplus storage expenses.
Make minimum order quantities work for you
Optimizing minimum order quantities (MOQs) can help businesses minimize inventory holding costs and improve overall profitability. By strategically managing MOQs, companies can reduce the amount of stock they need to store, leading to lower storage expenses and improved cash flow.
One way to make MOQs work for you is by negotiating with suppliers for lower minimum requirements. This enables you to order just enough inventory to meet customer demand without exceeding it, reducing the risk of overstocking.
Additionally, leveraging technology such as inventory management software can help you track sales patterns and forecast demand more accurately, allowing you to adjust your MOQs accordingly.
Avoid overstocking
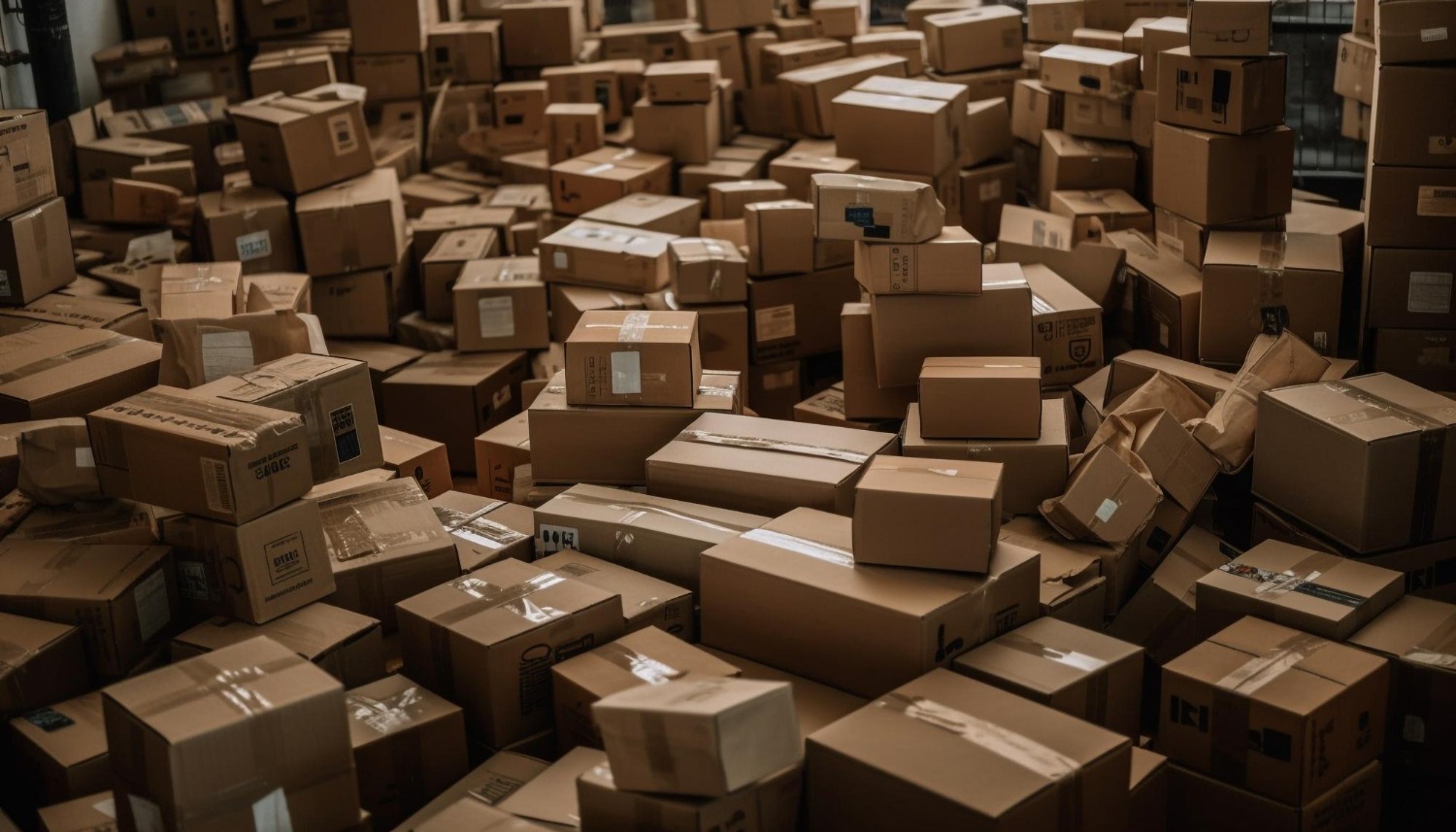
Overstocking can be a significant contributor to high inventory holding costs. When you have excess inventory sitting on your shelves, it ties up valuable capital and takes up precious storage space.
By avoiding overstocking, you can minimize stock carrying expenses and reduce inventory management expenses. It’s important to carefully analyze demand patterns and forecast future demand accurately to ensure that you order the right quantities of products at the right times.
Implementing efficient inventory management practices and utilizing data-driven insights can help you optimize your stock levels and avoid the costly mistake of overstocking.
Get rid of deadstock
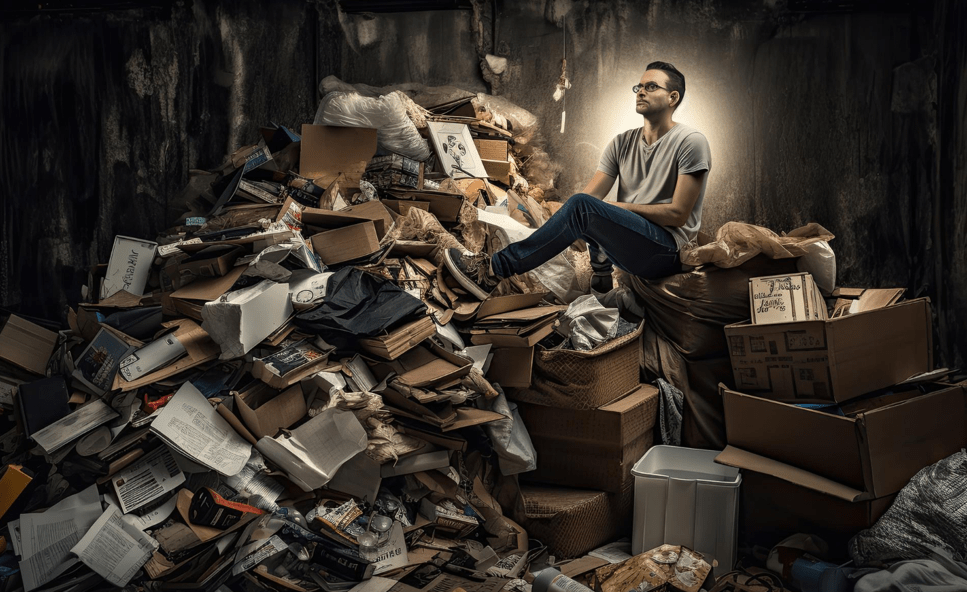
Eliminating deadstock is a crucial step in reducing inventory holding costs. Deadstock refers to products that are no longer in demand or outdated. By getting rid of deadstock, businesses can free up valuable storage space and avoid the expenses associated with holding onto unsellable items.
One effective way to get rid of deadstock is through markdowns or discounts to encourage customers to purchase these items. Another option is selling the deadstock inventory to liquidation companies or donating them for tax benefits.
It’s important for businesses to regularly assess their inventory and take proactive steps to remove any dead stock from their shelves.
Decrease supplier lead time
Decreasing supplier lead time is a crucial strategy to reduce inventory holding costs. When suppliers take longer to deliver the goods, it increases the time that inventory spends in storage and ties up valuable capital.
By working closely with suppliers and implementing measures such as vendor-managed inventory (VMI) or just-in-time (JIT) inventory management, businesses can ensure that products are delivered promptly.
This helps minimize stock holding costs, optimize warehouse efficiency, and improve overall supply chain performance. With shorter lead times, companies can respond more quickly to customer demands while reducing excess inventory and its associated carrying costs.
Use inventory management software
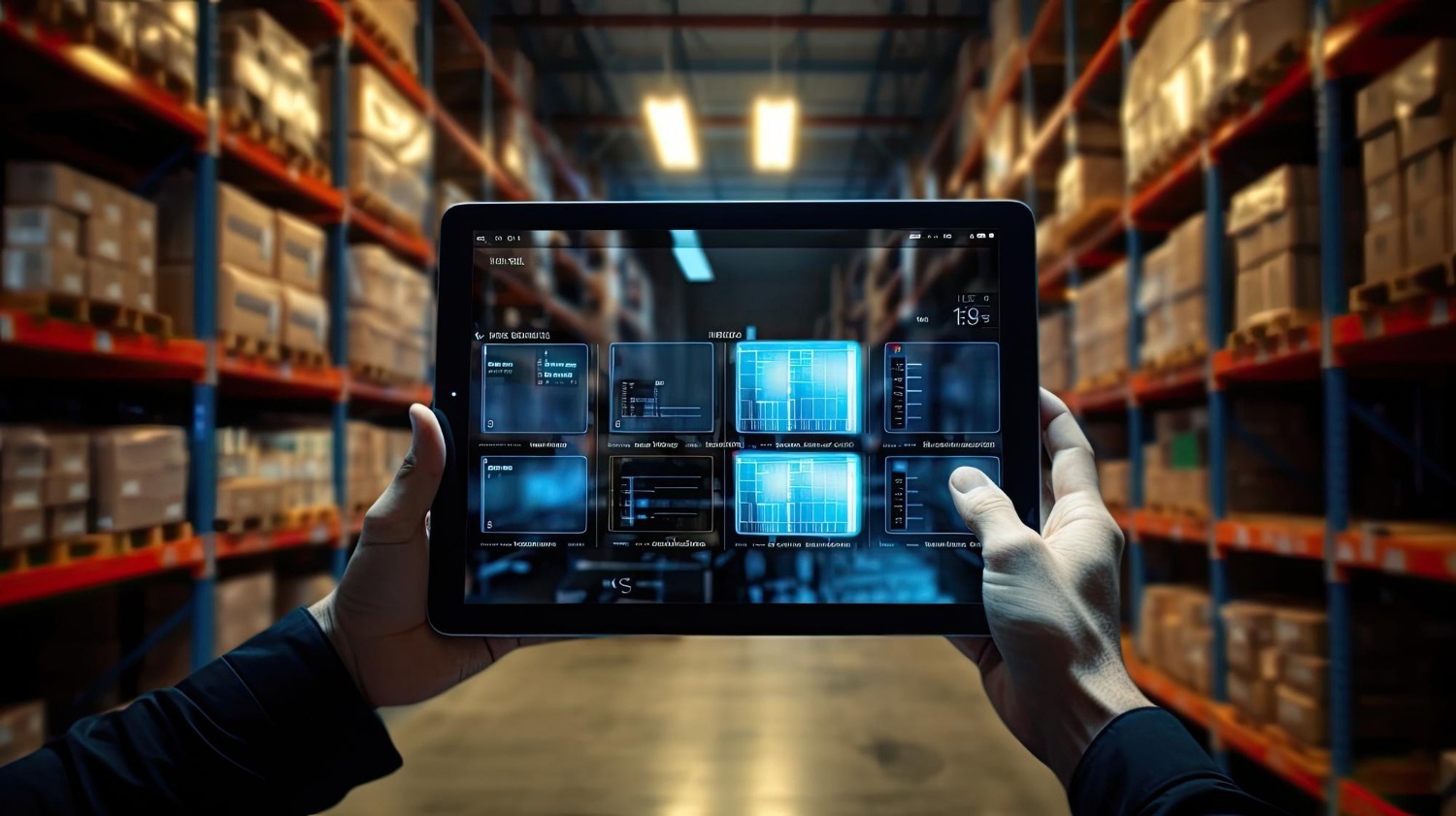
Utilizing inventory management software is a key strategy to reduce inventory holding costs. This software helps businesses keep track of their stock levels, ensuring they have the right amount of inventory on hand at all times.
With accurate data and real-time updates, companies can optimize their reorder points, minimizing the risk of overstocking or running out of essential items. Additionally, by using inventory management software, businesses can analyze historical sales data and forecast future demand accurately.
This allows for better planning and ordering decisions, reducing excess inventory and carrying costs. Furthermore, the software helps streamline supply chain operations by automating workflows such as order fulfillment and tracking shipments.
Understanding Inventory Holding Costs
Warehousing and logistics costs, insurance costs, materials handling costs, capital costs, storage costs, risk costs, and handling costs are all components that contribute to inventory holding costs.
Warehousing and logistic costs
Warehousing and logistic costs are a significant part of inventory holding costs. These costs include expenses related to storing and transporting goods, such as rent or lease for the warehouse, utilities, labor wages, packaging materials, transportation fees, and insurance.
To reduce these costs, businesses can optimize warehouse space utilization by organizing inventory efficiently and implementing proper storage systems. They can also negotiate better shipping rates with logistics providers or explore alternative transportation methods to minimize freight expenses.
By effectively managing warehousing and logistic costs, companies can lower their overall inventory holding expenses.
Insurance costs
Insurance costs are an important factor to consider when it comes to inventory holding costs. These costs can include insurance premiums and fees for insuring your inventory against theft, damage, or loss.
By evaluating your insurance coverage and shopping around for the best rates, you can potentially save a significant amount of money on insurance costs. Additionally, you can also explore options such as self-insurance or increasing deductibles to further reduce these expenses.
Lowering insurance costs is one of the ways businesses can effectively minimize their overall inventory holding expenses and improve their bottom line.
Materials handling costs
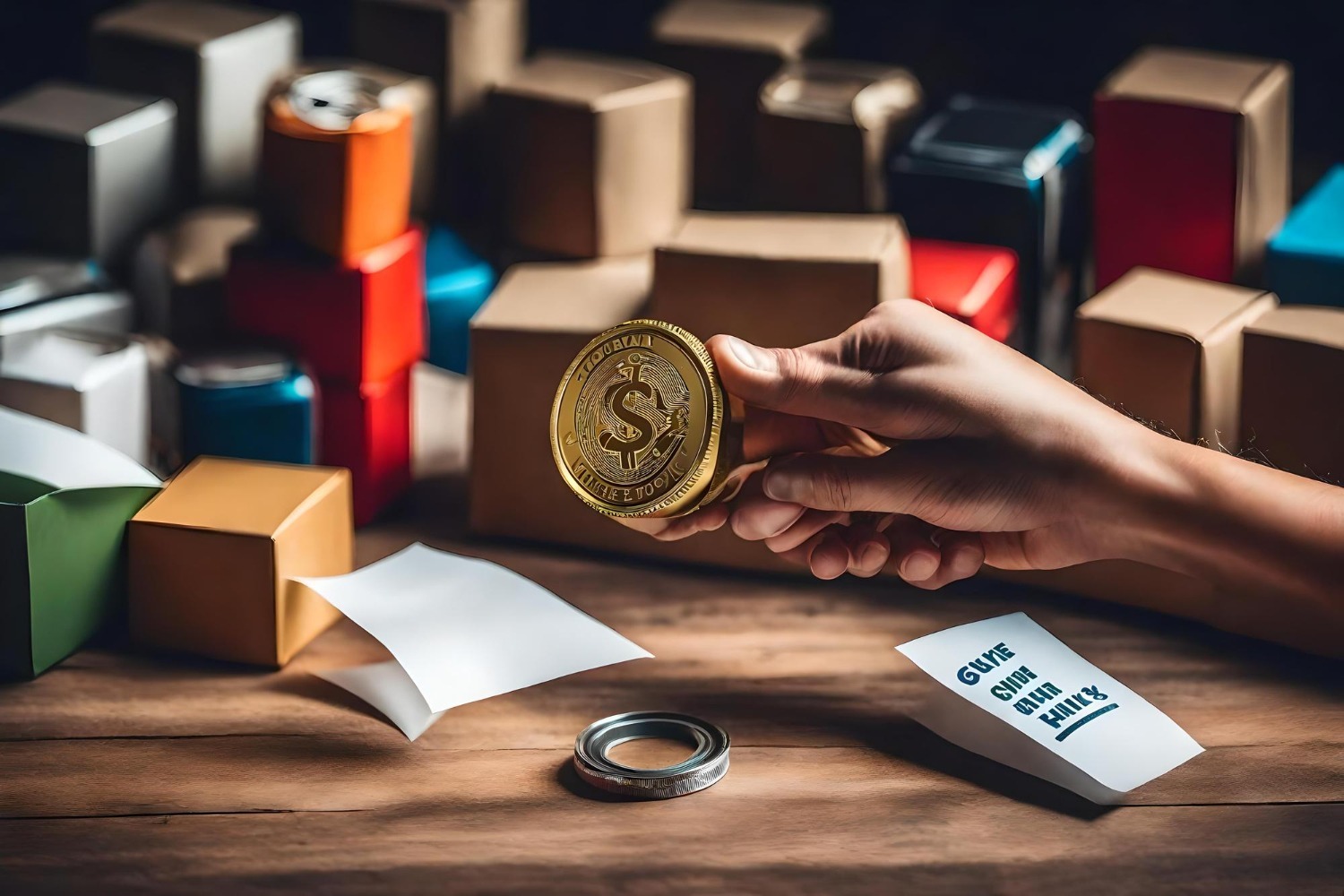
Materials handling costs refer to the expenses incurred in moving and transporting inventory within a warehouse or facility. This includes the cost of labor, equipment, and processes involved in receiving, storing, picking, packing, and shipping goods.
Efficient materials handling can help minimize these costs by optimizing workflow, reducing manual labor requirements, and streamlining operations. By implementing strategies such as automation technologies and layout redesigns that improve accessibility and reduce travel distances, businesses can lower their materials handling expenses while increasing productivity.
In addition to minimizing labor costs through efficient handling practices, investing in suitable equipment like forklifts or conveyors can also contribute to cost reduction. By using advanced material-handling technology and properly training staff on its use, companies can achieve faster order fulfillment times while reducing the risk of damage or loss during transportation.
Capital costs
Capital costs are a significant factor when it comes to inventory holding expenses. These costs include the initial investment required to purchase inventory, as well as the ongoing costs associated with financing and maintaining that inventory.
By carefully managing capital costs, businesses can reduce their overall inventory carrying costs and free up valuable resources for other areas of operation. This can be achieved by optimizing order quantities, improving cash flow management, and exploring alternative financing options such as consignment inventory or vendor-managed inventory (VMI) arrangements.
Lowering capital costs is an essential step in minimizing stock holding expenses and improving overall profitability.
Storage costs
Storing inventory can come with significant costs. Warehousing and logistic expenses, insurance fees, materials handling charges, capital costs, risk expenses, and handling fees all contribute to the overall cost of keeping stock on hand.
To minimize storage costs, it’s essential to optimize storage space efficiently and reduce excess inventory. By implementing effective inventory management practices and streamlining the supply chain, businesses can lower their stock holding expenses and decrease inventory storage costs.
Risk costs
Managing risk costs is crucial for reducing inventory holding expenses. These costs include potential losses due to theft, damage, obsolescence, and fluctuations in market demand. To minimize risk costs, businesses can implement strategies such as conducting regular inventory audits, improving security measures at warehouses, investing in insurance coverage for inventory, and staying updated with market trends to avoid holding obsolete or slow-moving stock.
By proactively managing risks associated with inventory holding, businesses can lower their overall expenses and improve their profitability.
Handling costs
Handling costs refer to the expenses associated with moving, storing, and managing inventory. These costs can include labor costs for handling and packaging products, as well as transportation costs for shipping items from one location to another.
To minimize handling costs, it is important to streamline inventory management processes and optimize storage space. By implementing efficient handling strategies and utilizing warehouse technology, businesses can reduce unnecessary expenses and improve overall efficiency in their supply chain operations.
It is essential to find ways to decrease these handling costs in order to lower inventory carrying expenses and maximize profits.
Calculating and Analyzing Inventory Holding Costs
To calculate inventory holding costs, you need to determine the types of holding costs involved and use the inventory holding cost formula.
Types of holding costs
There are several types of holding costs associated with inventory management. These include warehousing and logistic costs, insurance costs, materials handling costs, capital costs, storage costs, risk costs, and handling costs.
Warehousing and logistic costs refer to expenses related to storage facilities and transportation. Insurance costs cover the insurance premiums for protecting the inventory against potential losses or damages.
Materials handling costs involve expenses associated with moving inventory within the warehouse. Capital cost includes the interest paid on loans used to finance inventory purchases.
Storage cost refers to fees for storing goods in a warehouse or other storage facility. Risk cost accounts for potential losses due to theft or damage of inventory. Finally, handling cost encompasses labor expenses related to managing inventory such as receiving and shipping goods.
Inventory holding cost formula
To calculate inventory holding costs, you can use the following formula: Inventory Holding Cost = Average Inventory Value x Holding Cost Rate. The average inventory value is determined by adding the beginning and ending inventory values for a specific period of time and dividing by two.
The holding cost rate represents the percentage or dollar amount of carrying costs associated with each unit of inventory. By accurately calculating your inventory holding costs, you can identify areas where expenses are high and take steps to reduce them, such as improving inventory management or optimizing storage space.
Inventory holding cost calculation example
To better understand how inventory holding costs are calculated, let’s take a look at an example. Imagine you run a small retail store and have been keeping track of your holding costs for the past year.
First, you need to determine the types of costs that contribute to inventory holding expenses in your business. This includes warehousing and logistic costs, insurance costs, materials handling costs, capital costs, storage costs, risk costs, and handling costs.
Next, gather all the relevant data for the calculation. This will include information such as average inventory value over a specific period (let’s say one month), total annual holding cost rate (expressed as a percentage), and any additional fees or expenses related to storing and managing your inventory.
Strategies to Cut Inventory Holding Costs
Improve inventory management, streamline the supply chain, implement just-in-time (JIT) inventory management, forecast demand, and optimize storage space.
Improve inventory management
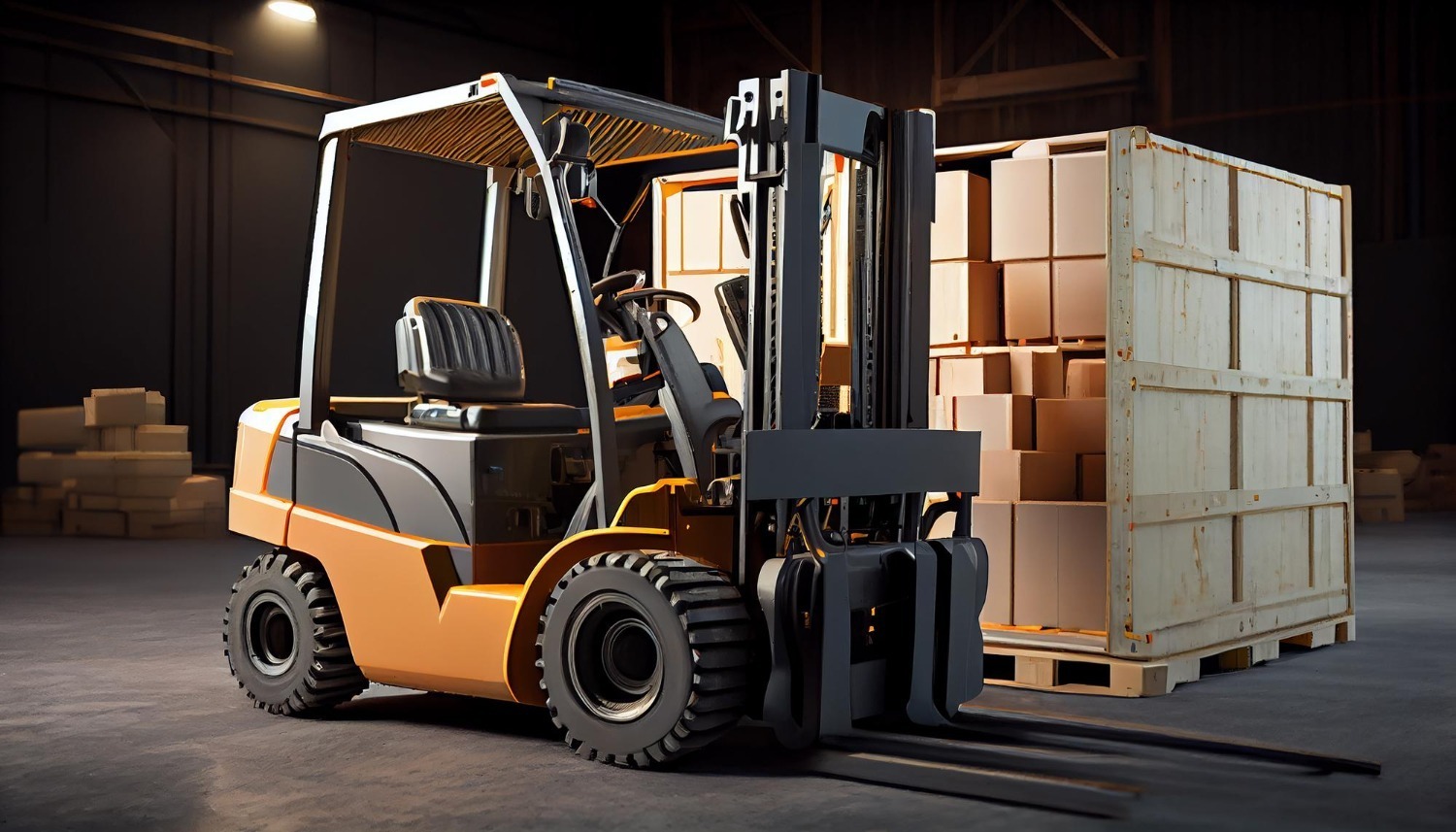
Improving inventory management is a key strategy to reduce holding costs and streamline operations. By implementing efficient inventory control systems, businesses can better track stock levels, avoid overstocking or stockouts, and optimize order fulfillment processes.
This includes using technology such as inventory management software to automate tasks like tracking inventory levels and generating reorder alerts. Additionally, adopting just-in-time (JIT) inventory management principles can help minimize excess stock and decrease storage expenses.
With improved inventory management practices in place, businesses can lower their overall holding costs while ensuring they have the right amount of stock on hand to meet customer demand efficiently.
Streamline the supply chain
To reduce inventory holding costs, it is essential to streamline the supply chain. This involves optimizing the flow of goods from suppliers to customers, minimizing delays and bottlenecks along the way.
By improving communication and coordination with suppliers, manufacturers can ensure timely deliveries and avoid stockouts or excess inventory. Implementing efficient transportation and logistics systems also helps in reducing lead times and lowering storage expenses.
Streamlining the supply chain enables businesses to minimize inventory carrying costs and improve overall cost efficiency.
Implement just-in-time (JIT) inventory management
Implementing just-in-time (JIT) inventory management can be an effective way to reduce inventory holding costs. JIT involves ordering and receiving inventory only when it is needed, minimizing the amount of excess stock that needs to be stored.
By having a precise understanding of customer demand and working closely with suppliers, you can ensure that the right quantity of materials or products arrives exactly when it is needed for production or order fulfillment.
This strategy helps to minimize storage and carrying costs associated with excess inventory, while also reducing the risk of obsolescence or loss due to damaged goods.
With JIT inventory management, you can optimize your supply chain by eliminating unnecessary lead times in procurement and production processes. By streamlining operations through efficient communication with suppliers and implementing strategies like vendor-managed inventory (VMI), you can decrease supplier lead time and enhance overall efficiency in material flow.
Forecast demand
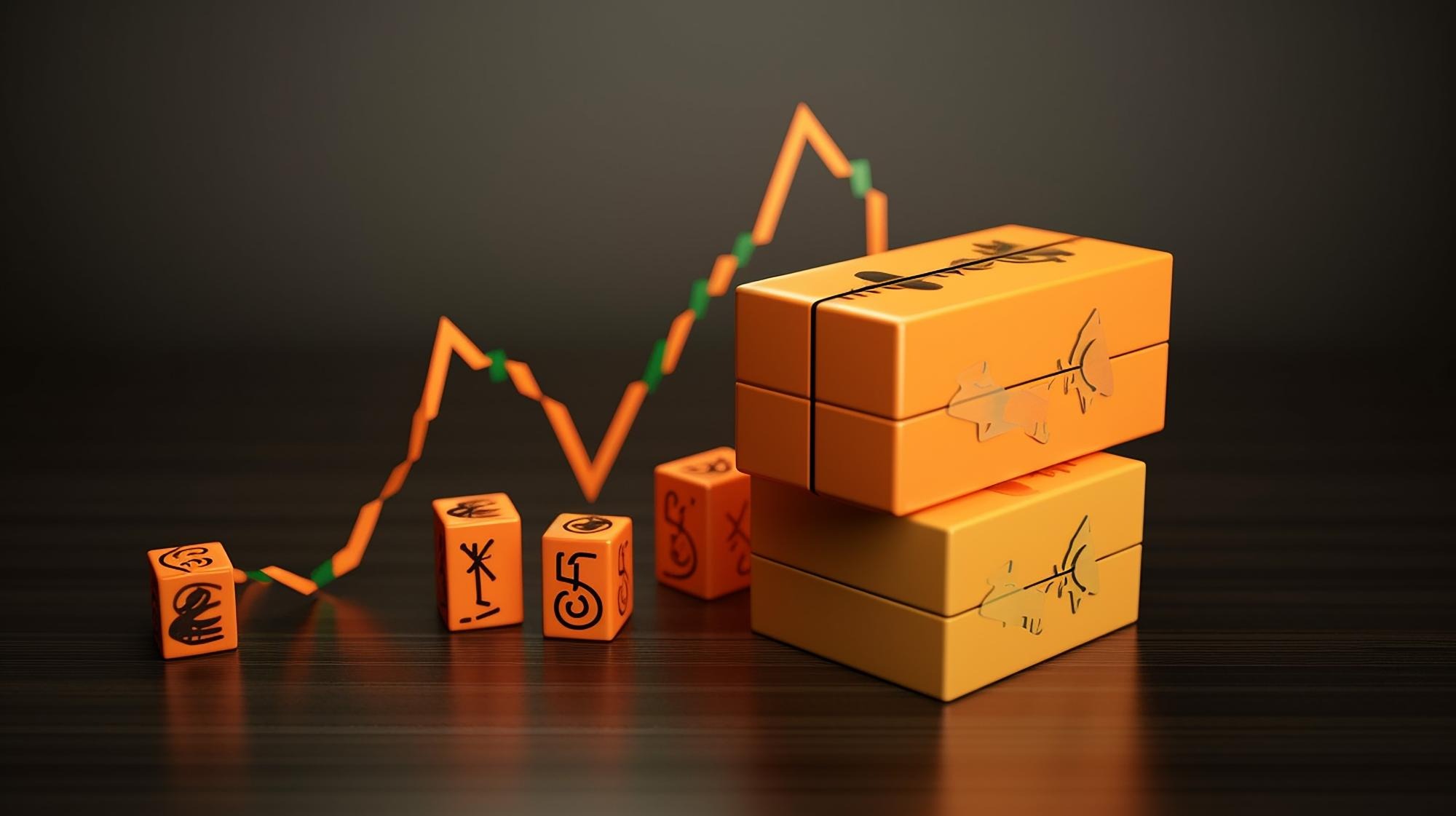
Forecasting demand is a crucial aspect of reducing inventory holding costs. By accurately predicting how much inventory will be needed in the future, businesses can avoid overstocking or understocking their products.
A thorough understanding of market trends, historical data, and customer behavior can help companies make informed decisions about inventory levels. Implementing reliable demand forecasting techniques can ultimately lead to optimized inventory management and lower overall expenses associated with carrying excess stock.
Optimize storage space
To lower inventory carrying costs, it is crucial to optimize storage space efficiently. By organizing and maximizing the available storage areas, you can minimize the need for additional warehouse or storage facilities.
Use vertical racking systems, pallets, and shelving units to make the most of the available space. Implementing a first-in-first-out (FIFO) system ensures that older inventory gets used before newer stock, reducing the risk of obsolescence.
Additionally, regular audits and reevaluation of the layout can help identify unused or underutilized spaces that can be repurposed for more efficient storage.
Conclusion
In conclusion, implementing effective strategies to reduce inventory holding costs can greatly benefit businesses. By optimizing inventory management, streamlining the supply chain, and forecasting demand accurately, companies can decrease storage expenses and lower overall carrying costs.
Utilizing tools like just-in-time inventory management and vendor-managed inventory can also help in minimizing stock holding expenses and improving warehouse efficiency. Taking these steps will ultimately lead to better cost reduction and improved profitability for businesses.
FAQs
What are some ways to reduce inventory holding costs?
You can minimize the storage expense by implementing strategies like Just-in-Time inventory, Lean manufacturing, and Vendor-managed inventory.
How does Just-In-Time (JIT) inventory help in reducing stock storage costs?
Just-In-Time inventory system allows retailers to order and receive goods only as needed, which reduces warehouse storage costs and minimizes the risk of overstocking items.
Can vendor-managed inventory (VMI) lower stock-holding costs?
Yes! With a VMI strategy, your supplier maintains your product levels which means you only hold what’s needed for sales or production, helping to decrease any unnecessary expenses related to excessive stockholding.
What role does Lean Manufacturing play in minimizing inventory holding expenses?
Lean Manufacturing focuses on reducing waste within a manufacturing system which often leads to cost reduction by eliminating unnecessary steps that contribute to high stock storage expenses.
Could improving my Stock Turnover rate benefit my business cost-wise?
Definitely! Higher stock turnover rates mean more frequent sales at lower storage costs – it contributes directly towards cost optimisation including reducing overall Inventory Holding Costs.