CNC programmers know the headache of adapting to different machines and reworking code. NCSIMUL 4CAM steps in with over two decades of development, easing these pains by bridging the gap between CAM systems and real-world machine execution.
Our article dives into how this powerful tool can transform your CNC programming, making it more efficient and error-free. Ready for smoother production?
Key Takeaways
- NCSIMUL 4CAM lets you easily switch part production between different CNC machines, saving time and reducing machine downtime.
- The software creates native CNC code that’s error – free, meaning less time spent fixing mistakes and rewriting programs for different machines.
- Features like real – time collision detection and automatic optimization of feeds and speeds help protect your equipment and speed up manufacturing.
- By integrating seamlessly with CAD/CAM systems, NCSIMUL 4CAM simplifies the transition from design to actual production.
- It offers a competitive advantage in discreet manufacturing by improving productivity, lowering operational costs, and ensuring high-quality output.
Enhancing CNC Programming with NCSIMUL 4CAM
NCSIMUL 4CAM revolutionizes CNC programming by offering flexibility and efficiency on the shop floor, ensuring error-free programming in native CNC code. With its notable features and benefits in discreet manufacturing industries, NCSIMUL 4CAM is a game-changer in the world of CNC technology.
Flexibility and Efficiency on Shop Floor
NCSIMUL 4CAM brings unparalleled flexibility to the shop floor, empowering machinists to switch part production between different CNC machines without missing a beat. Imagine being able to adapt on-the-fly when production schedules change or when unexpected machine downtime occurs; this is the reality with NCSIMUL 4CAM’s advanced toolpath reengineering capabilities.
The software not only optimizes existing CNC programs for new machine conditions but also slashes cycle times through savvy feed and speed optimization.
This level of efficiency means manufacturers can respond quickly and confidently to client demands, ensuring that tight deadlines are met with precision. Real-time collision detection safeguards the machinery, minimizing costly errors before they happen.
Each step in the process contributes to a leaner manufacturing operation where waste is cut down and productivity skyrockets. Next up: Discover how error-free programming in native CNC code becomes a game-changer with NCSIMUL 4CAM.
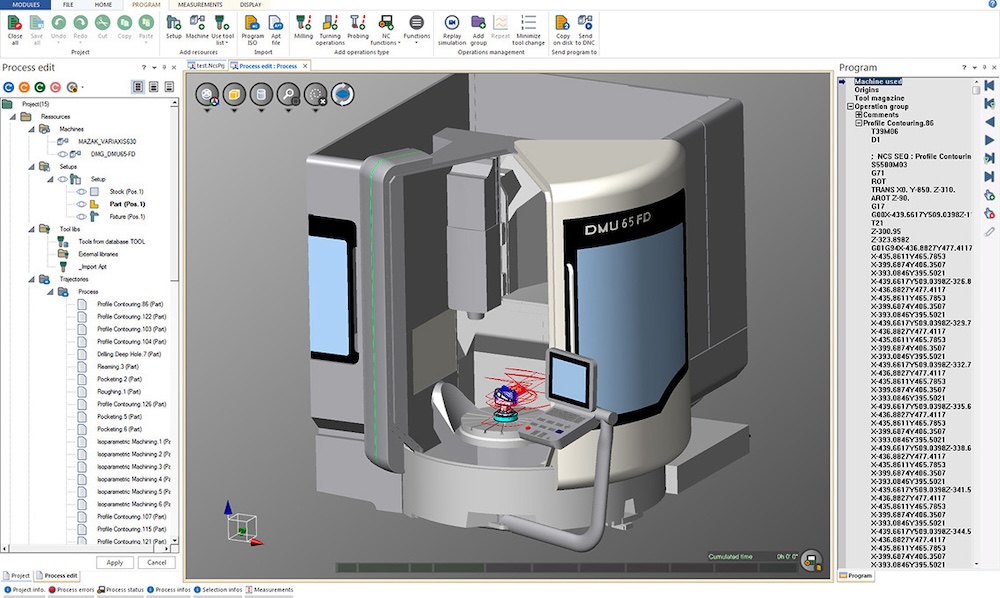
Error-free Programming in Native CNC Code
Picture this: you’re programming a CNC machine, and the code just flows without hiccups. That’s what happens when you use NCSIMUL 4CAM. It’s like having an expert by your side, ensuring your programming is spot-on every time.
The software takes over the tricky task of generating native CNC codes that machines understand immediately. This means no more backtracking to find errors or rewriting programs for different machines.
Imagine switching machines on the fly without stressing over program compatibility; NCSIMUL 4CAM makes it possible with its dynamic rest material management and hybrid programming features.
Now, legacy programs integrate effortlessly, aligning perfectly with new projects regardless of the target machine. Your shop floor turns into a hub of efficiency where error-free native CNC coding becomes standard practice, and productivity soars as if on wings.
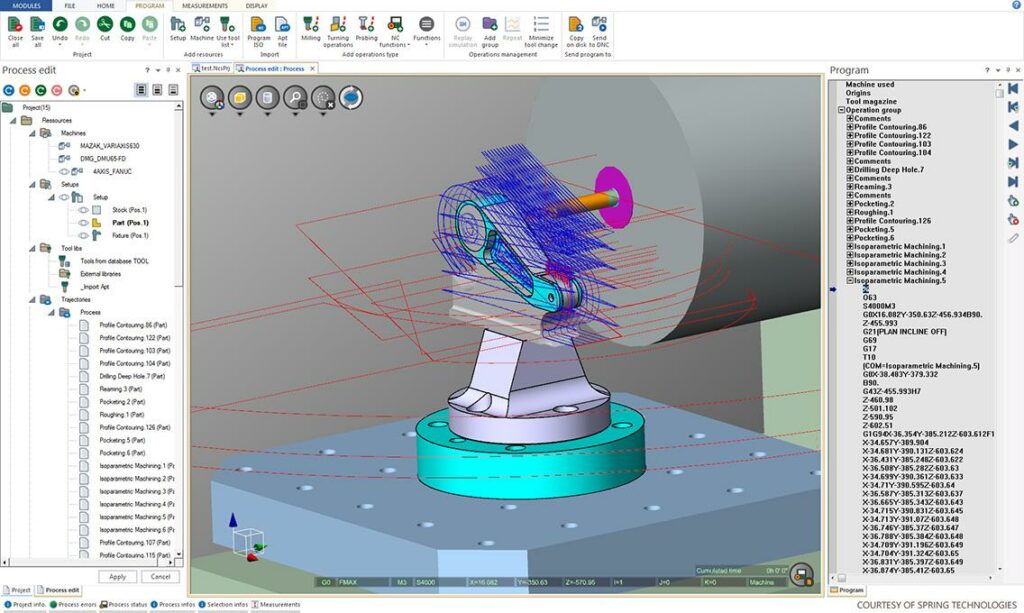
Notable Features of NCSIMUL 4CAM
NCSIMUL 4CAM stands out with its robust features designed to enhance CNC programming. These features streamline manufacturing processes and ensure the production of high-quality parts.
- Real-time CNC collision detection safeguards equipment by predicting and preventing potential crashes during simulation.
- Optimization of cutting tool feeds and speeds maximizes efficiency and reduces wear on machinery, saving time and resources.
- Seamless CAD/CAM integration allows for easy import of existing toolpaths and machining data, simplifying the transition from design to production.
- Error-free programming in native CNC code eliminates translation errors common with third-party postprocessors, ensuring machines operate as intended.
- Dynamic rest material management visualizes remaining material in real-time, supporting precision in subsequent machining passes.
- Hybrid programming capability facilitates the recovery of legacy programs, merging older data with new technology effortlessly.
- Automatic generation of new machine programs translates CAD files directly into machine-ready code without manual intervention, drastically reducing setup times.
- Flexibility to switch part production between different CNC machines enhances shop floor productivity by allowing quick responses to changing production demands.
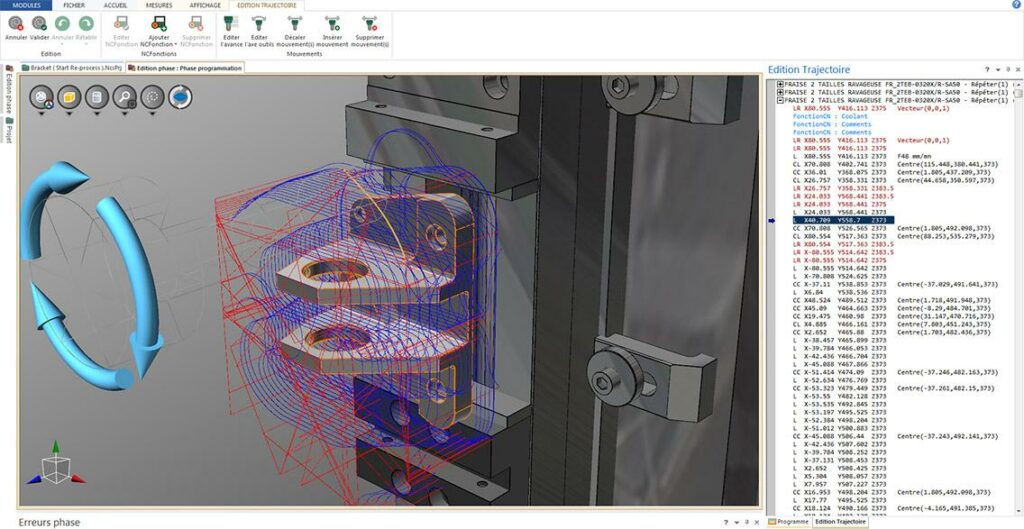
Benefits of NCSIMUL 4CAM in the Discreet Manufacturing Industry
Transitioning from the notable features of NCSIMUL 4CAM, it’s essential to delve into the tangible benefits that this software brings to the discreet manufacturing industry. By seamlessly generating new CNC machine programs and switching part machining between different CNCs without reprogramming, NCSIMUL 4CAM streamlines production processes and eliminates unnecessary downtime.
The dynamic rest material management feature ensures optimal utilization of resources, while its “Hybrid” programming facilitates seamless recovery of legacy programs. With error-free native CNC code programming and integration with various CAM solutions, businesses can significantly enhance productivity, reduce operational costs, and maintain a competitive edge in today’s manufacturing landscape.
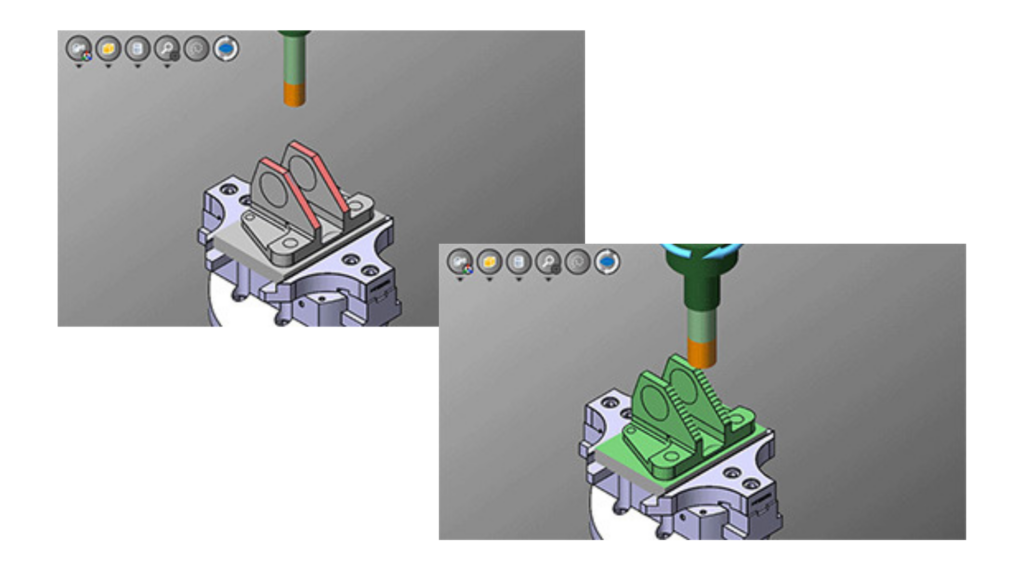
Conclusion
Revolutionize CNC programming with NCSIMUL 4CAM. Streamline production, eliminate errors, and optimize toolpaths effortlessly. Enhance your manufacturing efficiency with this cutting-edge software solution.
Embrace the power of NCSIMUL 4CAM and stay ahead in the competitive world of CNC technology. Elevate your CNC programming to new heights with NCSIMUL 4CAM – the ultimate industry game-changer!
(Image Source: ncsimul.com)