Are you wrestling with a disorderly warehouse that’s putting a damper on your productivity? Trust me, it’s not just you.
Turns out there’s even research to back this up – improving workflow efficiency through tactical layout planning can skyrocket order fulfilment rates by up to 50%. Exciting, right? So let’s help turn things around for your storage area.
This article is packed with helpful tips and critical factors to keep in mind while designing a kickass warehouse structure, one that promises optimal use of space.
Key Takeaways
- Budget considerations play a crucial role in designing an efficient warehouse layout, balancing affordability and efficiency.
- Maximizing available space through careful planning can significantly improve warehouse storage capacity and inventory management.
- Flow optimization focuses on reducing unnecessary movements and enhancing productivity by streamlining processes within the warehouse.
- Ensuring accessibility in the warehouse layout improves efficiency, reduces errors, and enhances overall productivity.
- Strategic equipment placement optimizes workflow and maximizes space utilization in the warehouse.
Principles for an Efficient Warehouse Layout Design
Budget considerations, available space, flow optimization, accessibility, and equipment placement are key principles to consider when designing an efficient warehouse layout.
Budget considerations
Budgeting plays a crucial role in designing an efficient warehouse layout. The available funds determine the kind of equipment you can obtain, the extent of space optimization, and the level of technology and automation to be incorporated into your warehouse system.
You need to consider costs related to facilities, distribution centre facility costs, labour costs, storage space/cube, and slots among others while sketching out your budget. It’s essential to strike a balance between affordability and efficiency: investing too little might lead to inefficiency; overspending can strain resources elsewhere in the business.
Available space
Investigating the available space is a vital step in designing an efficient warehouse layout. It’s not just about how much square footage you have, but also how that area is configured.
Some spaces may present challenges due to irregular shapes or obstructions like pillars and low ceilings. Yet even these can be overcome with creative warehouse design and layout strategies.
Maximizing storage capacity in warehouse layouts demands careful planning. You want to ensure paths are wide enough for equipment operation while making use of vertical space for stacking items, when appropriate.
A high ceiling might give room to install taller shelving units, effectively increasing your available inventory storage without expanding the floor plan. Even small adjustments can lead to significant improvements in efficient warehouse space planning!
Flow optimization
Flow optimization plays a fundamental role in achieving an efficient warehouse layout. It involves considering the complete journey of a product, from when it enters the warehouse to its final destination and every step in between.
An optimized flow can reduce unnecessary movements, decrease congestion and unwanted friction among employees, enhance productivity and contribute significantly to overall operational excellence.
Prioritizing product rotation and traffic flow plans actively shapes a smoother sequence for goods movement within your facility. This focus on streamlining processes ensures that orders are filled at quicker rates while simultaneously maximizing space usage through strategic placement of storage systems and equipment selection based on material handling needs – all contributing factors toward improved logistics operations through flow optimization in your warehouse design planning process.
Accessibility
When designing an efficient warehouse layout, accessibility is a critical factor to consider. An accessible layout ensures that employees can easily navigate the warehouse and retrieve items without any obstacles or delays.
This includes designing clear pathways between storage areas, organizing products in a logical order for quick retrieval, and implementing proper labelling and signage for easy identification.
By prioritizing accessibility in the warehouse layout design, businesses can optimize efficiency, reduce errors, and improve overall productivity.
Equipment Placement
Efficient equipment placement is a crucial aspect of designing a warehouse layout. By strategically placing equipment such as forklifts, conveyors, and storage racks, you can optimize the workflow and maximize space utilization.
Consider factors like accessibility, safety requirements, and traffic flow when deciding where to position equipment within the warehouse. This not only improves efficiency but also enhances overall productivity by minimizing time wasted on unnecessary movements.

Importance of a Practical Warehouse Layout Design
An efficient warehouse layout design is crucial for the smooth and productive operation of a warehouse. The layout directly impacts factors such as workflow, productivity, and safety within the facility.
A practical warehouse layout ensures that products can be easily accessed, stored, and moved throughout the space. It maximizes storage capacity and optimizes the flow of goods from receiving to shipping.
By designing a well-planned layout, businesses can improve order fulfilment rates, reduce errors in picking and packing, minimize travel time for workers, and enhance overall efficiency.
A practical warehouse layout also considers safety measures by providing clear pathways for pedestrians and separating areas for loading/unloading. Additionally, it allows for easy accessibility to equipment and minimizes unnecessary movements.
To achieve an effective warehouse layout design, businesses should consider factors such as available space, budget constraints, equipment needs, and personnel accessibility requirements while adhering to lean principles.
Regular evaluation of the layout is necessary to adapt to changing business needs such as seasonal fluctuations or new product lines. With proper planning and consideration of these factors in mind during the warehouse layout design process, businesses can streamline their operations and improve overall productivity in their warehouses.
Key Factors to Consider in Warehouse Layout Design
When designing a warehouse layout, there are several key factors to consider. These include budget constraints, available space, equipment needs, and personnel accessibility. By carefully considering these factors, businesses can create an optimized layout that maximizes efficiency and productivity.
Budget
Considering the budget is a crucial aspect when designing an efficient warehouse layout. It is important to determine how much you are willing to invest in the layout design, as it will impact various components such as equipment selection and space utilization.
By setting a budget, you can prioritize your resources and make informed decisions that align with your financial constraints. It also helps in identifying cost-effective solutions and ensures that your warehouse layout design remains within the allocated budget throughout the process of implementation and optimization.
A well-managed budget allows for strategic planning, maximizes return on investment, and contributes to overall efficiency in warehouse operations.
Space availability
Space availability is a key factor to consider when designing an efficient warehouse layout. Having enough space is essential for storing inventory and ensuring smooth flow of goods within the facility.
It is important to assess the available space and create a layout that maximizes storage capacity while allowing for easy movement of personnel and equipment. By optimizing space utilization, businesses can enhance efficiency and productivity in their warehouse operations.
Equipment needs
Selecting the right equipment is a vital factor in designing an efficient warehouse layout. It is important to consider the type of products being stored and handled, as well as the workflow within the warehouse.
Equipment such as forklifts, pallet racks, conveyors, and shelving units should be chosen based on their compatibility with the inventory and their ability to optimize storage space.
Additionally, considering automation technology can greatly improve efficiency by reducing errors and increasing productivity. Regular evaluation of equipment needs ensures that the warehouse remains adaptable to changing business demands and keeps operations running smoothly.
In summary: Selecting suitable equipment that aligns with inventory needs and workflow optimization is crucial for an efficient warehouse layout design. This includes considering factors such as product compatibility, storage space optimization, and implementing automated technology when appropriate.
Personnel accessibility
Personnel accessibility is a crucial aspect of designing an efficient warehouse layout. Easy access for employees to different areas within the warehouse promotes smooth operations and reduces unnecessary movement.
This can be achieved by strategically placing workstations, break rooms, restrooms, and other facilities close to where they are needed most. By ensuring that personnel have convenient access to their work areas, productivity can be maximized while minimizing time wasted on traveling throughout the facility.
Moreover, clear paths and proper signage should be implemented to guide employees efficiently throughout the warehouse.
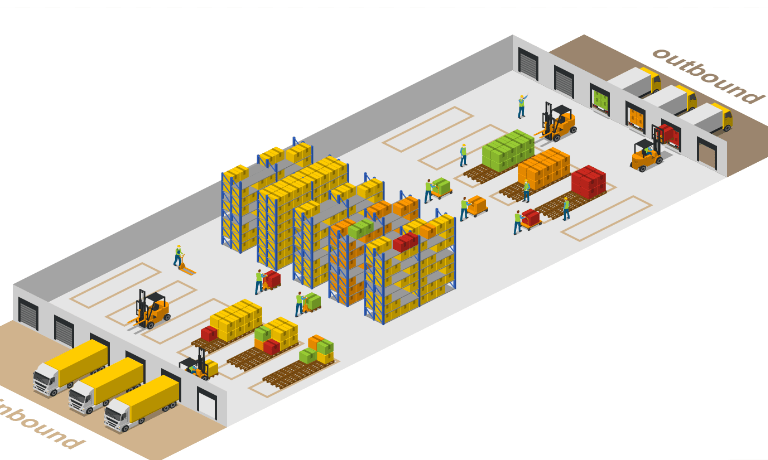
Tips for Designing an Efficient Warehouse Layout
Map out the space to determine the optimal layout for your warehouse, taking into consideration factors such as product flow, equipment placement, and personnel accessibility.
Map out the space
To design an efficient warehouse layout, it is essential to start by mapping out the available space. This involves creating a detailed diagram or floor plan that outlines the dimensions and features of the warehouse.
By accurately mapping out the space, you can identify potential areas for optimization and determine how best to utilize every square foot. This process allows you to visualize the flow of products, establish designated areas for different functions (such as receiving, storage, picking, and shipping), and ensure that there is adequate space for equipment and personnel movement.
Mapping out the space provides a solid foundation for designing an organized and well-optimized warehouse layout.
Optimize space usage
An efficient warehouse layout is all about maximizing space utilization. With careful planning and strategic design, you can optimize the available space in your warehouse to its fullest potential.
By organizing storage areas effectively, utilizing vertical space, implementing efficient racking systems, and considering traffic flow patterns, you can ensure that every inch of your warehouse is put to good use.
This not only maximizes your storage capacity but also improves overall workflow efficiency, making it easier for employees to locate items quickly and reducing the time required for order fulfilment.
Choose suitable equipment
In designing an efficient warehouse layout, it is crucial to choose suitable equipment. Selecting the right equipment for your warehouse operations can greatly impact productivity and overall efficiency.
Consider factors such as the type of goods being handled, the volume of products, and any specific requirements or constraints within your warehouse space. By choosing equipment that is appropriate for your needs, you can ensure smooth and streamlined operations, minimize errors, improve safety measures, and maximize storage capacity.
Stay up-to-date with advancements in automation and technology to explore opportunities for increased efficiency in equipment selection.
Test and record results
Testing and recording results is a crucial step in designing an efficient warehouse layout. By conducting tests, we can evaluate the effectiveness of the layout design and identify any areas that need improvement.
This can include testing different traffic flow plans, equipment placements, and storage configurations to ensure optimal efficiency and productivity. Recording the results allows us to track progress over time, make necessary adjustments, and implement best practices for future warehouse layouts.
Additionally, it helps us gather valuable data on order fulfilment rates, inventory analysis, and overall warehouse performance. Regular testing and record-keeping are essential for continuous improvement in warehouse operations.
Consider various layout designs
When designing an efficient warehouse layout, it is important to consider various layout designs. The choice of layout design can greatly affect the flow and efficiency of operations within the warehouse.
Some common layout designs include U-shaped layouts, straight line layouts, and cross-docking layouts. Each layout has its own advantages and considerations, so it’s essential to evaluate which design best suits your specific needs and goals.
By considering various layout designs in your warehouse planning process, you can optimize space utilization, improve workflow efficiency, and enhance overall productivity.
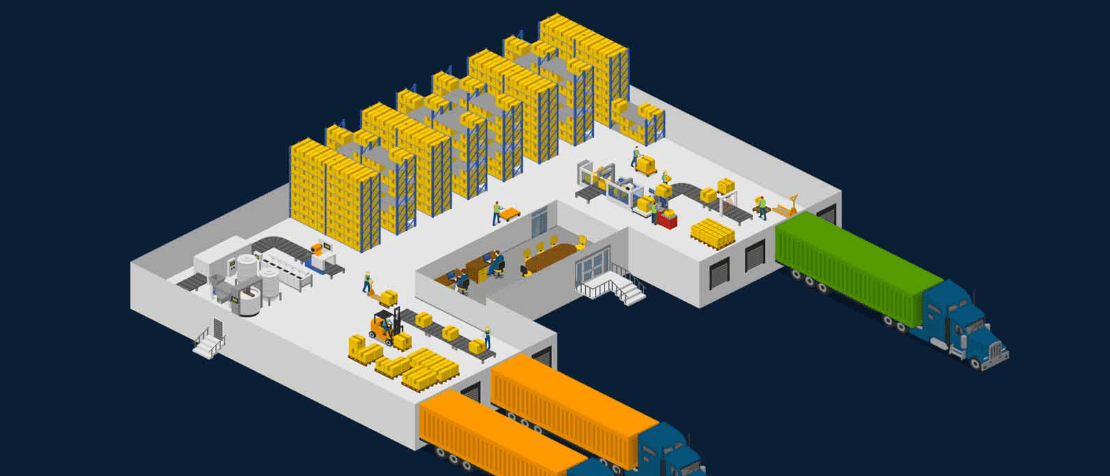
Conclusion
In conclusion, designing an efficient warehouse layout is crucial for optimizing productivity and streamlining operations. By considering factors such as flow optimization, equipment placement, and accessibility, businesses can create a practical layout that maximizes space utilization and enhances workflow efficiency.
Regular evaluation and adjustment of the warehouse layout are necessary to adapt to changing business needs and ensure ongoing operational excellence.
Frequently Asked Questions
Why is an efficient warehouse layout important?
An efficient warehouse layout is important because it maximizes storage space, reduces operational costs, and improves productivity by minimizing movement and optimizing workflows.
What factors should be considered when designing a warehouse layout?
When designing a warehouse layout, factors to consider include the type of products being stored, size and weight of inventory, expected order volume, equipment used for handling goods, and safety regulations.
How can I optimize the flow of goods in my warehouse?
To optimize the flow of goods in your warehouse, you can use techniques such as implementing logical product organization systems, using barcode or RFID technology for inventory tracking, creating designated pick and pack areas, and utilizing automation where possible.
Can I make changes to my existing warehouse layout without disrupting operations?
Yes, changes can be made to an existing warehouse layout without disrupting operations by carefully planning the transition process. This may involve gradually moving sections of inventory or temporarily relocating certain activities until the changes are complete.
Are there any software tools available to help with designing an efficient warehouse layout?
Yes, there are various software tools available that can assist with designing an efficient warehouse layout. These tools provide features like virtual modeling capabilities and optimization algorithms to help visualize different layouts and determine the most effective configuration for your specific needs.