I discovered that manufacturers added an astonishing $2.91 trillion to the U.S. economy just in Q1 2023! Quite mind-boggling.
How manufacturers make money and they amass such astronomical income and what are some critical financial ratios to be aware of?
Key Takeaways
- Manufacturers generate income through various methods such as advertising, sponsorship, subscription models, and licensing and royalties.
- Key financial ratios like inventory turnover, revenue per employee ratio, total manufacturing costs per unit minus materials, return on net assets, and unit contribution margin ratio are crucial in assessing the performance and profitability of manufacturing companies.
- Manufacturing companies use different production methods including Make to Stock (MTS), Make to Order (MTO), and Make to Assemble to meet market demand and optimize efficiency.
- Understanding these factors is essential for anyone involved in the manufacturing industry or interested in investing.
Key Financial Ratios for Manufacturing Companies
Manufacturing companies utilize several key financial ratios to assess their performance, including inventory turnover, revenue per employee ratio, total manufacturing costs per unit minus materials, return on net assets, and unit contribution margin ratio.
Inventory Turnover
Inventory turnover is a key financial metric that manufacturing companies pay close attention to. It’s all about determining how often a manufacturer can sell its inventory during a specific period, like one year.
A higher turnover rate generally indicates that a company is efficiently producing and selling goods. Why does this matter? Because it directly impacts profitability by revealing the amount of investment tied up in inventory against the revenue from sales.
For instance, let’s say we have two manufacturers with similar operations and income levels; however, one has twice the inventory as the other. The one with less inventory will likely realize higher returns due to lower operating expenses and increased efficiency in delivering products to customers — hence having better cash flow dynamics! Therefore, consistently monitoring inventory turnover helps businesses ensure they’re not over or under-producing— optimizing their production efficiency for maximum profit potential.
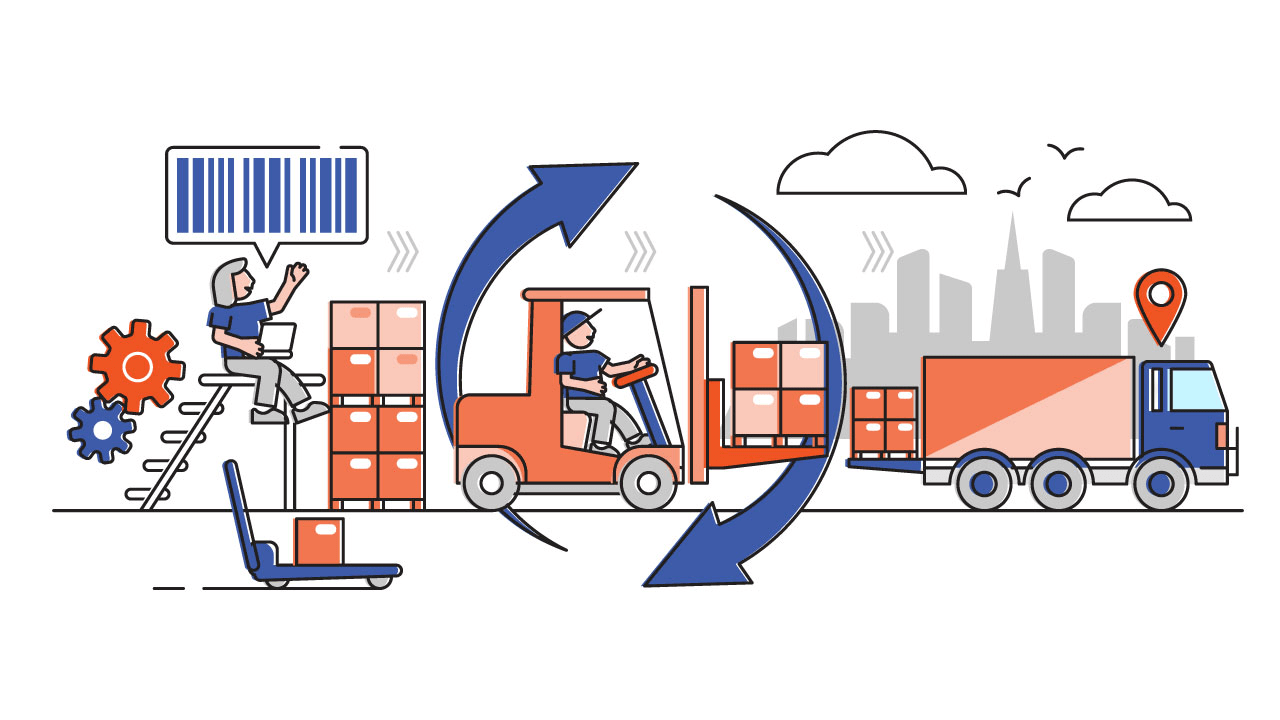
Revenue Per Employee Ratio
Efficiency in the manufacturing industry can be measured using the Revenue Per Employee Ratio. This financial ratio gives a snapshot of how well a company is utilizing its workforce to generate income.
For instance, if Company A produces $500,000 in revenue with 50 employees and Company B generates the same amount with just 35 employees, then Company B has a higher Revenue Per per-employee ratio and is more efficient at converting personnel costs into sales.
A high Revenue Per revenue-per-employee ratio often signals better productivity within an organization. It could mean that the company’s operations are streamlined or it may employ advanced technologies leading to reduced labor costs per unit of output.
To illustrate, manufacturers contributed $2.91 trillion to the U.S. economy in Q1 2023 partly attributed to improved efficiencies in production processes achieved by both large corporations and emerging biopharmaceutical companies through economies of scale and technological innovations respectively.
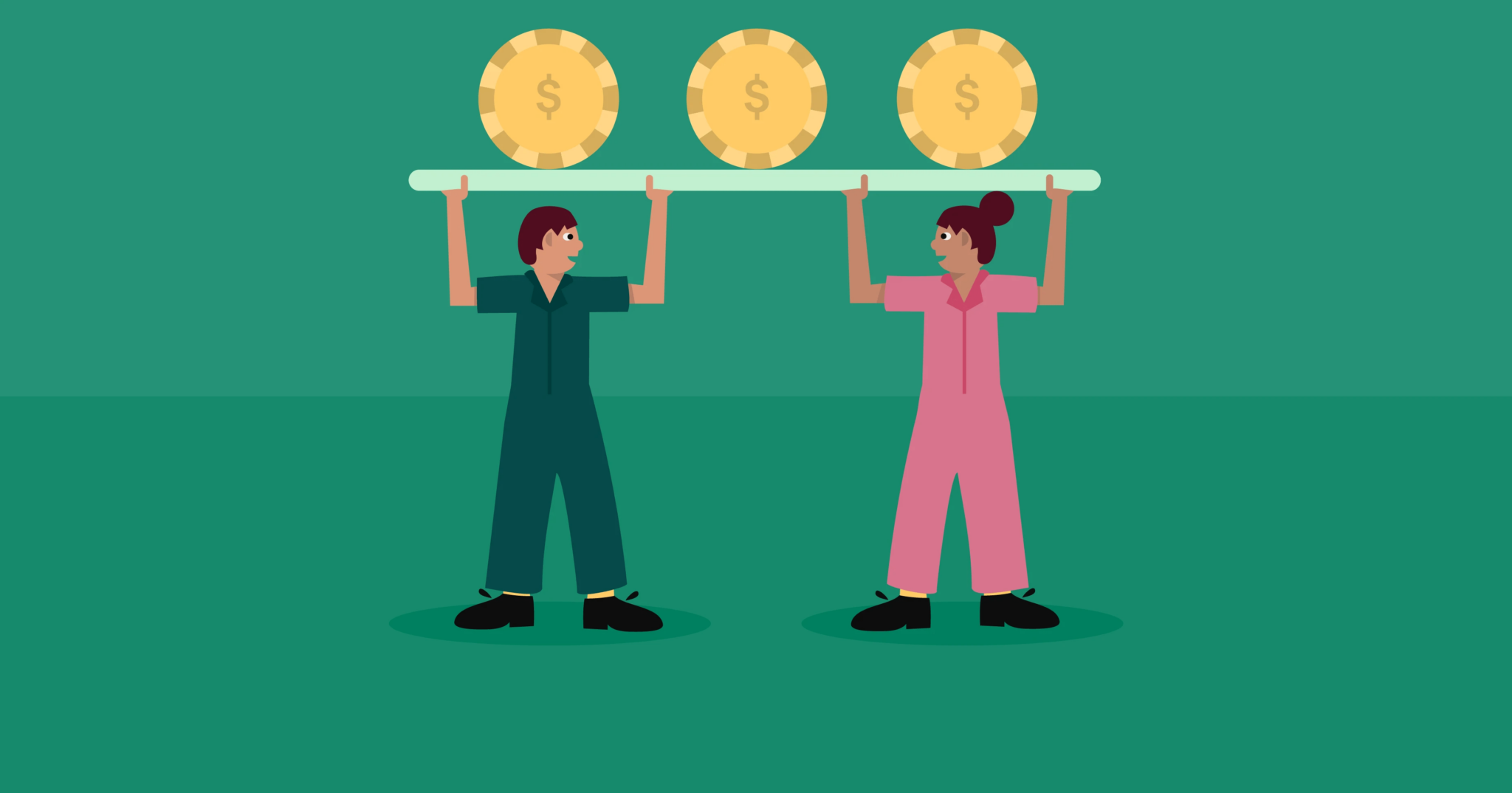
Total Manufacturing Costs Per Unit Minus Materials
Manufacturing costs per unit include both direct and indirect costs. Direct costs correlate directly with production, including raw materials and labour. These are easy to calculate since they’re tied directly to the product output.
Indirect manufacturing costs, also known as overhead or fixed costs, might not be as obvious but still play a significant role in overall cost calculations. They comprise everything else that contributes to making the product but isn’t part of the actual goods – things like rent for the factory building, utilities, or salaries for non-production staff.
Now to get total manufacturing cost per unit minus materials (also called Conversion Cost), you simply subtract material cost from the total cost per unit. This metric is crucial in finance’s role in manufacturing as it allows manufacturers and potential investors to ascertain production efficiency over time or across different products while eliminating the price fluctuation impact of raw materials.
Even with economies of scale benefits prevalent among larger companies where increased production quantity reduces average cost per unit made possible by spreading overheads over more units produced; accurate tracking of this conversion cost helps improve the decision-making process on sales and marketing strategy alongside setting realistic profit goals.
In essence, understanding how manufacturers make money requires an intricate understanding of these numbers which contributes greatly towards business profitability assessment through financial performance analysis techniques like calculating gross margin – obtained by deducting total manufacturing cost from revenue generated.
Find the Best Financial Analysis software to calculate and seamlessly manage financial ratios for your company.
Return on Net Assets
Return on Net Assets is a financial ratio that measures a manufacturing company’s profitability by comparing its net income to the value of its assets. It provides insights into how effectively the company is using its assets to generate profits.
A higher return on net assets indicates better efficiency and performance in utilizing resources to generate income. This ratio helps investors and stakeholders evaluate the company’s ability to generate returns on investments and make informed decisions about their involvement with the company.
For manufacturers, focusing on improving this ratio can lead to increased profitability and business sustainability.
Unit Contribution Margin Ratio
The unit contribution margin ratio is a key financial ratio used by manufacturing companies to analyze their profitability. It calculates the percentage of each unit’s sales price that contributes to covering fixed costs and generating profit.
By subtracting the variable costs per unit from the selling price per unit, manufacturers can determine how much money is left over to cover fixed expenses and contribute towards profit.
This ratio helps businesses make informed decisions about pricing strategies, cost control measures, and overall financial performance.
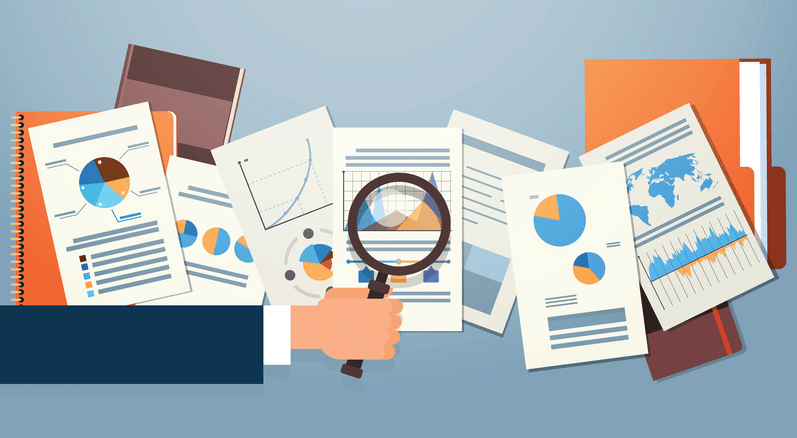
Types of Manufacturing Production
Manufacturing companies use different production methods to meet market demand and optimize efficiency. These include Make to Stock (MTS), Make to Order (MTO), and Make to Assemble.
Make to Stock (MTS)
Make to Stock (MTS) is a manufacturing production method where goods are produced based on anticipated customer demand. In MTS, products are made and stocked in advance, ready for immediate purchase by customers.
This approach allows manufacturers to respond quickly to market demands and ensure products are readily available for customers. By analyzing historical sales data and market trends, companies can accurately forecast the quantity needed to meet future demand.
This proactive strategy helps minimize stockouts and maximize customer satisfaction. Manufacturers using the MTS approach often benefit from economies of scale, as they can produce goods in large quantities, resulting in lower unit costs.
Make to Order (MTO)
Make-to-order (MTO) is a manufacturing production method where products are only made once the customer places an order. This means that goods are not produced in advance, but instead, they are manufactured according to specific customer requirements.
MTO allows for customization and flexibility, as each product is tailored to meet individual customer needs. By using the MTO approach, manufacturers can avoid holding excess inventory and reduce the risk of unsold goods sitting on shelves.
It also helps control costs by minimizing storage expenses and reducing the likelihood of obsolete stock. Manufacturers benefit from this model by being able to respond quickly to changing market demands while maintaining efficient production processes.
Make to Assemble
In the manufacturing industry, there are different types of production methodologies that companies use. One of these methods is “make to assemble.” This approach involves producing components or parts of a product based on anticipated demand, and then assembling them into the final product when orders are received.
By doing this, manufacturers can reduce inventory costs and lead times since they only produce what is needed for assembly. This method requires careful planning and coordination with suppliers to ensure timely delivery of component parts.
It also allows for customization options based on customer preferences. Make-to-assemble production offers flexibility and efficiency in meeting customer demands while optimizing resources and minimizing waste.
How Manufacturing Companies Generate Income
Manufacturing companies generate income through various methods such as advertising and sponsorship, subscription models, and licensing and royalties.
Advertising and Sponsorship
Advertising and sponsorship play key roles in generating income for manufacturing companies. By advertising their products and services through various media platforms, manufacturers can reach a wide audience and increase brand visibility.
Through sponsorships, they can establish partnerships with other businesses or events to further promote their brand. These strategies not only drive sales but also help create brand loyalty among consumers.
With effective advertising and strategic sponsorships, manufacturing companies can boost revenue and enhance their overall profitability in the competitive market.
Subscription Models
Manufacturing companies have found success in implementing subscription models as a way to generate income. By offering subscriptions, manufacturers can provide customers with regular access to their products or services for a recurring fee.
This allows for a steady stream of revenue and builds customer loyalty. Subscription models are particularly popular in industries such as software, where companies offer monthly or yearly subscriptions for access to their programs or online platforms.
Manufacturers benefit from this model by ensuring ongoing customer engagement and predictable revenue streams.
Additionally, subscription models can also serve as a way for manufacturers to gather valuable data on customer preferences and behaviour. With each subscription, companies can collect information that helps them tailor their offerings and marketing strategies to better meet the needs of their target market.
This data-driven approach allows manufacturers to make informed business decisions and improve profitability.
Licensing and Royalties
Manufacturing companies have additional streams of income through licensing and royalties. This means they grant permission to other businesses or individuals to use their intellectual property, such as patents, trademarks, or copyrights, in exchange for a fee called royalties.
These fees are typically based on a percentage of the revenue generated from the licensed product or service. Licensing and royalties can be a significant source of income for manufacturing companies, especially if they have unique technology or innovative products that others want to utilize.
It allows them to expand their reach and profits beyond their own manufacturing capabilities.
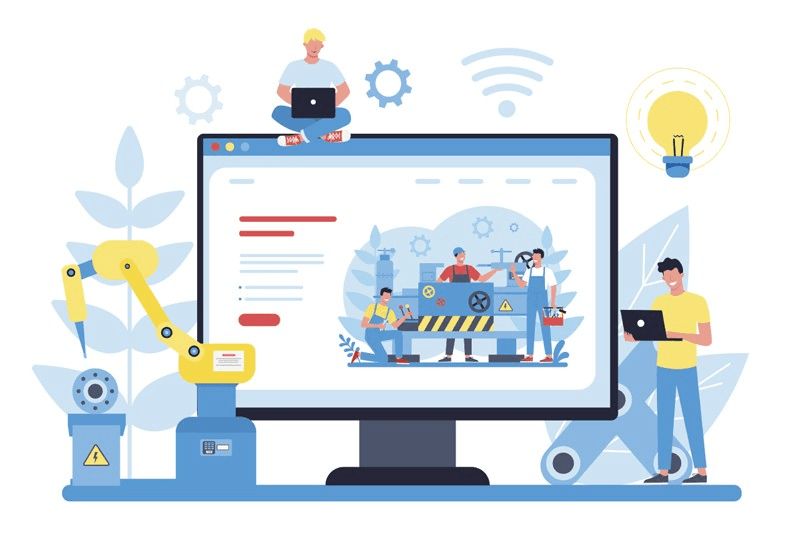
Conclusion
Understanding how manufacturers make money is crucial for anyone involved in the industry or interested in investing. By analyzing key financial ratios and exploring different types of manufacturing production, we can gain insights into their revenue generation strategies.
Additionally, understanding how manufacturers generate income through methods like advertising and sponsorship helps us understand the business profitability of these companies. By delving into these factors, we can better comprehend the intricacies of the manufacturing industry and its role in driving economic growth.
Frequently Asked Questions
How do manufacturers make money?
Manufacturers make money by producing and selling products at a higher price than the cost of production.
What factors affect a manufacturer’s profitability?
A manufacturer’s profitability is influenced by factors such as production costs, pricing strategies, market demand, competition, and efficiency in operations.
Can manufacturers earn money from sources other than product sales?
Yes, manufacturers can earn additional income through services like maintenance and repair of their products, licensing agreements, or royalties from intellectual property.
Are all manufacturing industries equally profitable?
No, the profitability of manufacturing industries varies depending on factors such as competition levels, market demand for the products they produce, and their ability to control costs and operate efficiently.
How can understanding how manufacturers make money benefit consumers?
Understanding how manufacturers make money can help consumers make informed decisions about purchasing products by evaluating whether the price reflects the value offered and whether there are any alternative options available in terms of quality or cost.